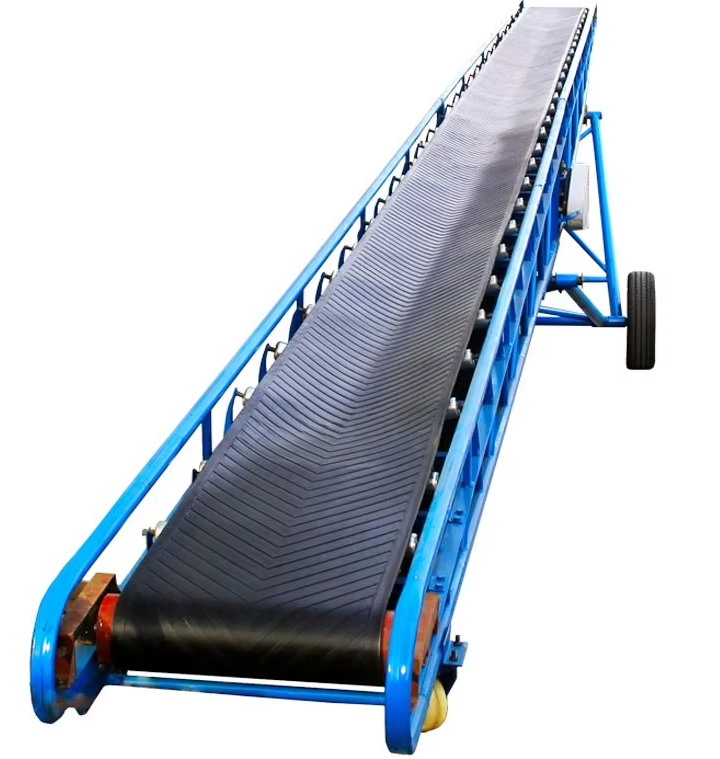
Conveyor belt for abrasive materials
Conveyor belt for abrasive materials refers to a belt conveyor device specially designed for continuous conveying of highly abrasive, granular or powdered abrasive materials. It has high wear resistance, tear resistance and impact resistance and is widely used in sandstone, sandblasting, grinding materials, metallurgical powder and other industries.
Product Introduction
Conveyor belt for abrasive materials is an industrial belt conveyor device specially designed for conveying high-hardness, highly abrasive bulk abrasive particles. It has excellent wear resistance, tear resistance and impact resistance. It is widely used in abrasive processing, sandblasting systems, metallurgy, glass, casting and other industries for continuous transportation of abrasives. With a flexible substrate as a carrier, abrasive particles are fixed by bonding, sintering or electrostatic sand planting to form a belt tool with directional grinding ability. Its core function is to drive the conveyor belt to circulate through the equipment, so that the abrasive and the workpiece surface produce relative friction.
What is the main function of the conveyor belt for abrasive materials?
Conveyor belt for abrasive materials is a conveying system designed for transporting abrasive particles. Its core functions are:
Efficient conveying: conveying abrasives of different mesh sizes from the storage bin to the processing equipment (such as polishing machine, belt sander).
Precise sorting: ensure the uniformity of abrasive particle size through vibrating screen or air flow sorting.
Wear-resistant design: rubber, polyurethane or metal mesh belt is used to withstand abrasive friction and impact.
Video of conveyor belt for abrasive materials
What is the structure of conveyor belt for abrasive materials?
The structure of conveyor belt for abrasive materials is specially designed to cope with the high hardness and high abrasiveness of abrasive. Although the basic components are similar to ordinary conveyor belts, there are significant differences in material selection and structural details. The typical conveyor belt for abrasive materials structure consists of a cover layer, a belt core (fabric core, fabric core (), an intermediate rubber layer, etc.
Characteristics of conveyor belt for abrasive materials
Uniform distribution of abrasives: The particles need to be evenly fixed on the conveyor belt for abrasive materials to avoid local accumulation or sparseness leading to uneven grinding effect and affecting the surface quality of the workpiece.
Strength and wear resistance: The substrate needs to withstand the tension and friction during the conveying process. It usually adopts a multi-layer fiber reinforced structure with a tensile strength of 100~300N/mm.
Multi-layer composite structure: usually high-strength fiber fabric (such as polyester, nylon) or rubber, providing the basic strength and flexibility of the conveyor belt to ensure that it is not easy to deform or break during the transmission process.
Integrated molding process: The abrasive particles are firmly combined with the substrate through processes such as coating, pressing or sintering to form a rough grinding working surface while maintaining the continuous transmission characteristics of the conveyor belt.
Technical parameters of conveyor belt for abrasive materials
Parameters |
Key indicators |
Application recommendations |
Material |
Rubber, polyurethane, metal mesh, magnetic belt |
High hardness abrasives choose metal mesh, micro Powder selection anti-static belt |
Mesh range |
60 mesh (250μm) to 3000 mesh (5μm) |
Select low mesh for coarse grinding and high mesh for fine grinding |
Conveying speed |
0.5-5m/s |
High speed (>3m/s) is suitable for light abrasives |
Tilt angle |
≤15° |
The larger the tilt angle, the more belt friction is required |
Environmental adaptability |
High temperature resistance, corrosion resistance, anti-static |
Select high temperature resistant belt for ceramic processing and anti-static belt for semiconductors |
Basic characteristics of abrasives
Abrasives are used for grinding, lapping, polishing, sandblasting High-hardness granular or powdered materials used in the processing of, etc., have extremely strong abrasiveness.
Common abrasive types:
Natural abrasives: quartz sand, corundum, natural diamond
Artificial abrasives: brown corundum, white corundum, silicon carbide, aluminum oxide powder, ceramic sand
Recommended mesh number of conveyor belt for abrasive materials
The particle size of the abrasive has a direct impact on the conveying method, usually expressed as "mesh number (mesh)", which is inversely proportional to the particle size.
Particle size grade |
mesh number range |
corresponding particle size (μm) |
Application example |
Coarse abrasive |
8 ~ 24 mesh |
> 710 μm |
Sandblasting, deburring, regrinding |
Medium abrasive |
36 ~ 80 mesh |
180 ~ 500 μm |
Polishing pretreatment, surface cleaning |
Fine abrasive |
100 ~ 240 mesh |
50 ~ 150 μm |
Fine grinding, mirror processing pretreatment |
Micro powder abrasive |
320 mesh or more |
< 45 μm |
Precision grinding, ceramic polishing, ultra-precision machining |
The influence of mesh on conveyor belts
The mesh of abrasive directly affects the selection and design of conveyor belts:
Low mesh (coarse particles, such as 60-120 mesh): The particles are large, the impact force is strong, and the wear is mainly scratches and impact pits. The conveyor belt needs to have a thick wear-resistant layer (such as high-strength rubber or ceramic composite materials), and may adopt a modular design for partial replacement.
Medium mesh (such as 150-240 mesh): The particles are moderate, and wear and friction coexist. Conveyor belts need to balance wear resistance and flexibility, and multi-layer composite materials are often used.
High mesh (fine particles, such as 400 mesh and above): The particles are fine and easy to form abrasive dust, and the wear is mainly surface abrasion. The conveyor belt needs to have anti-adhesion and dust-proof functions, and the surface may use special coatings (such as PTFE) to reduce dust accumulation.
Application of conveyor belt for abrasive materials
Conveyor belts for abrasive materials are indispensable in specific scenarios such as sandblasting, sand belt/sandpaper manufacturing, mining stone processing, metal casting shot blasting cleaning, and glass/ceramic wet grinding due to their wear resistance, impact resistance, and adaptability to the high hardness, sharpness, and particle size diversity of abrasives.
Industry |
Application point |
Conveying materials |
Sandblasting equipment factory |
Sandblasting recovery system, sand box return |
Quartz sand, corundum |
Abrasive manufacturing plant |
Grading and conveying of raw sand after crushing |
Brown corundum, alumina powder |
Foundry industry |
Molding sand, waste sand recovery system |
Quartz sand, resin sand |
Glass factory |
Sandblasting, polishing powder delivery |
Quartz powder, abrasive powder |
Carbide processing |
Abrasive delivery between coarse grinding and fine grinding |
Micro-powder grade silicon carbide or aluminum oxide |
Coated abrasive factory |
Automatic feeding and conveying system for abrasives in sandpaper production line |
Abrasive particles of various grades |
Price of conveyor belt for abrasive materials
The price of conveyor belt for abrasive materials is affected by many factors, including brand, specification, material, abrasive type and mesh number.
By specification: the larger the width, the higher the price. As the length increases, the price rises accordingly. Usually the price is calculated by meter, and the common lengths are 1 meter, 2 meters, 5 meters, etc. The unit price per meter of long-sized conveyor belts may have certain discounts.
By material: abrasive conveyor belts with polyester non-woven fabric as the base material are relatively cheap, while those with rubber or high-strength fiber fabric as the base material are more expensive.
By abrasive mesh number:
Low mesh number (coarse grinding): such as abrasive conveyor belts with about 80 mesh, the price is relatively low.
High mesh number (fine grinding): fine grinding conveyor belts with more than 400 meshes will also increase in price due to higher requirements for abrasive processing accuracy.
In actual purchases, it is also necessary to choose a suitable abrasive conveyor belt based on specific usage needs and budget. At the same time, factors such as purchase quantity, transportation cost, and after-sales service will also have a certain impact on the final price.