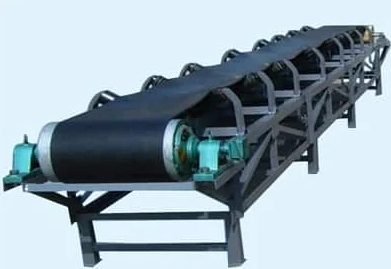
Conveyor belt for wet materials
Conveyor belt for wet materials is mainly used for pipeline conveying of wet or viscous materials, such as sludge, wet coal, mud, wet materials in food processing, etc. This type of pipeline belt needs to have the characteristics of waterproof, corrosion-resistant, wear-resistant and easy to clean to meet the special requirements of wet material conveying.
What is a conveyor belt for wet materials?
Conveyor belt for wet materials is a belt conveyor system that is water-resistant, corrosion-resistant, and has good structural closure. It is used for continuous conveying of materials with poor fluidity, high viscosity, easy to drip or easy to contaminate. This equipment is specially used for conveying systems of materials with high moisture content (such as wet mud, wet sand, sludge, wet grain, etc.). In industrial applications, it is often used in scenes such as sewage treatment, mine dehydration, food processing, and agricultural waste treatment. Compared with ordinary conveyor belts, they have undergone some special treatments in material and structure to deal with problems such as moisture and adhesion to ensure the effective conveying of materials.
What types of conveyor belt for wet materials are there?
Conveyor belt for wet materials is a special equipment used in industrial production to convey wet, sticky or liquid materials. It is widely used in chemical, food, mining, sewage treatment and other industries. The following are common types of conveyor belt for wet materials:
Type |
Water-resistant rubber conveyor belt |
PVC/PU conveyor belt |
Metal mesh belt |
Sidewall baffle conveyor belt |
Spiral conveyor belt |
Features |
Surface covered with water-resistant rubber layer |
Corrosion-resistant, easy to clean |
Stainless steel material, corrosion-resistant and breathable |
With sidewalls and baffles |
Pushing materials through spiral blades |
Image |
|
|
|
|
|
Application |
Prevent moisture penetration from causing belt delamination |
Applicable to food or chemical wet materials (such as seafood, sauces, etc.) |
Suitable for high temperature and high humidity environments (such as washing lines, drying lines) |
Prevent wet materials from slipping or leaking (such as sludge, slurry transportation) |
Used for high viscosity wet materials (such as mud, feces) |
Conveyor belt for wet materials video
What is the working principle of the conveyor belt for wet materials?
Challenges of conveyor belts for wet materials
In many industrial environments, conveyor belts are essential for efficiently moving materials. However, when operating in wet conditions, these conveyor belt systems can face a number of challenges that affect their performance and reliability.
Reduced traction: Wet conditions can cause a significant reduction in traction between the conveyor belt and the drive pulley, which can cause slippage, resulting in reduced productivity and increased wear on the conveyor belt and other components.
Corrosion: Exposure to wet conditions can accelerate corrosion of metal components on wet material conveyor belt systems, weakening the structure and shortening its service life.
Material buildup: Wet material can adhere to the conveyor belt, causing buildup and blockage. This not only reduces the capacity of the conveyor belt, but also increases the risk of damage to the conveyor belt for wet materials and increases downtime for cleanup.
Belt aging: Continued exposure to wet conditions can cause the conveyor belt material to age, resulting in cracks, tears, and other forms of damage, requiring more frequent replacement.
How to deal with problems faced by conveyor belts for wet materials?
Apply a non-slip coating: Applying a non-slip coating to the drive pulley and other contact surfaces can increase traction and reduce slippage in wet conditions.
Choose the right conveyor belt material: Choosing a conveyor belt material that is resistant to moisture and corrosion can significantly improve its performance in wet conditions. Or choose to include rubber belts with special coatings, or synthetic materials designed to resist moisture.
Install a belt cleaning system: Regularly cleaning the conveyor belt can help prevent material buildup and reduce the risk of belt damage, such as scrapers, brushes, and high-pressure water jets.
Improve drainage systems: This can be achieved by installing gutters, drain covers, or shields to protect the conveyor belt for wet materials from rain and other sources of moisture.
Practice preventive maintenance: Regularly inspect and maintain the conveyor system, including checking for signs of corrosion, belt wear, and material buildup, and promptly repairing and replacing them.
Technical specifications of conveyor belt for wet materials
Parameters |
Technical specifications |
Parameters |
Technical specifications |
Belt width |
50-200 cm (common specifications: 50 cm, 80 cm, 100 cm, 120 cm, 160 cm, 200 cm) |
Material |
PU, silicone, Teflon, rubber, stainless steel mesh belt, modular plastic |
Conveying capacity |
30-3000 t/h |
Belt speed |
0.5-4 m/s |
Angle |
0°-90° |
Material density |
0.5-2.5 t/m³ |
Material moisture content |
10%-85% |
Temperature range |
-60℃ to +260℃ |
Surface design |
smooth surface, anti-slip pattern, corrugated rib/skirt, diaphragm |
Abrasion resistance |
Abrasion loss ≤100 mm³ (wear-resistant rubber/ceramic coating) |
Corrosion resistance |
acid and alkali resistance |
cleaning method |
scraper/brush |
Service life |
1-5 years |
environmental adaptability |
temperature: -19℃ to +40℃ |
Auxiliary device |
vibration device, deviation correction system, sealing cover, dust collector |
safety standard |
food grade |
Talk about the application of wet material conveyor belt
Conveyor belt for wet materials is specially designed for high humidity, viscosity, liquid or water-permeable materials, and is widely used in food, mining, chemical, environmental protection and building materials industries.
Industry |
Typical materials |
Recommended conveyor belt types |
Core requirements |
Food |
Fish, shrimp, sauces |
Stainless steel mesh belt |
PU belt Hygienic, easy to clean |
Mining |
Wet ore, mud |
Rubber belt + wire rope core |
Heavy load resistance, non-slip |
Environmental protection |
Sludge, wet garbage |
Spiral conveyor belt/Fully enclosed PU belt |
Anti-corrosion, anti-odor |
Chemical |
Resin, pulp |
Teflon belt/316 stainless steel belt |
Chemical corrosion resistance |
Conveyor belt for wet materials selection suggestions
Learn the characteristics of the conveyed materials in detail.
Clarify the requirements of the conveying system.
Select the appropriate conveyor belt for wet materials type and material according to the material and system requirements.
Select the appropriate conveyor belt structure and configuration.
Consider the professionalism and after-sales service of the supplier.
Customer cases of conveyor belt for wet materials
Case |
Fruit and vegetable washing conveyor line |
Wet granulation production line |
Manure conveyor in livestock and poultry farms |
Image |
|
|
|
Problem |
Starch on the surface of some fruits and vegetables adheres to the conveyor belt, causing blockage and cross contamination |
The powder and adhesive have high viscosity after mixing, and the conveyor belt is prone to residual materials |
Wet manure is very sticky, and traditional conveyor belts are prone to slip and wear quickly |
Solution |
Use Teflon coated conveyor belt to reduce starch adhesion |
Use stainless steel mesh belt, the open hole design accelerates water evaporation |
Use rubber pattern conveyor belt to increase friction |
Effect |
Transportation efficiency increased by 40%, and washing water consumption reduced by 25% |
Material residue rate reduced to less than 1% |
Conveyor belt life extended by 1.5 times, manual cleaning costs reduced by 30% |